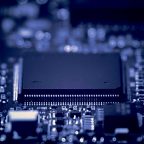
Künstliche Intelligenz
Selbstlernende Maschinen nutzen Big Data und Cloud-Computing, um laufend die abhängigen Prozesse zu optimieren. von Andreas Fuhrich Ob künstliche Intelligenz, … Künstliche Intelligenz weiterlesen
Selbstlernende Maschinen nutzen Big Data und Cloud-Computing, um laufend die abhängigen Prozesse zu optimieren. von Andreas Fuhrich Ob künstliche Intelligenz, … Künstliche Intelligenz weiterlesen
In praxisnahen „Forschungsfabriken“ können neue Verfahren getestet werden – unter anderem am KIT in Karlsruhe. Testen, entwickeln, forschen weiterlesen
Der 5G-Standard: Grundvoraussetzung für das Industrial IoT 5G: Steuerung ohne Latenz weiterlesen
Digitalisierung des Remote Supports im industriellen Service von Alina Kaspers und Martin Riedel Hersteller von komplexen Maschinen und Anlagen sind … Plattformen im Field-Service weiterlesen
Das IoT wird zum KI-Datenlieferanten: Durch die Algorithmen des maschinellen Lernens entstehen so neue Produkte, Prozesse und Services. Datenbasierte Geschäftsmodellinnovationen weiterlesen