Bestehende Maschinen werden zum Maschinenpark 4.0.
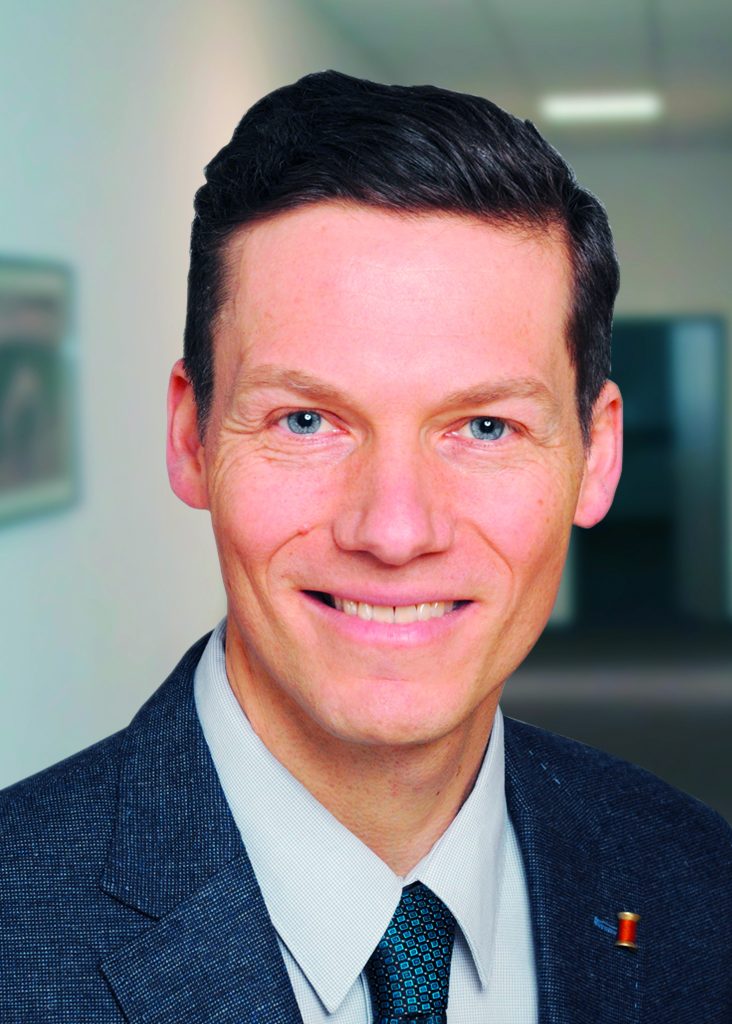
von Lumir Boureanu
Es gibt verschiedene Gründe, warum heute Maschinenparks aufgerüstet und modernisiert werden. Maschinen werden häufig für einen bestimmten Zweck angeschafft, der sich jedoch im Laufe des Lebenszyklus durchaus ändert. Maschinen müssen dann angepasst oder erweitert werden. Ziel unserer Kunden ist es zum Beispiel, eine Verlängerung der Maschinen-Lebensdauer, die Produktqualität und die Versorgung mit Ersatzteilen im Maschinenpark sicherzustellen. Aber digitaler Retrofit für Bestandsanlagen bedeutet im Kontext von Industrie 4.0 (IIoT) für uns noch mehr.
Gehen wir davon aus, dass nicht alle Maschinen die neusten Schnittstellen besitzen und noch analog ihre Dienste verrichten. Zusätzlich treffen wir bei der Beratung unserer Kunden immer wieder auf heterogene Maschinenlandschaften verschiedenster Hersteller und teilweise stammen Spezialmaschinen noch aus den 70er-Jahren.
Aber Digitalisierung erfordert nicht unbedingt neue Maschinen. Mit den richtigen Lösungen lassen sich heterogene Maschinenparks harmonisieren und für das IIoT vorbereiten. Voraussetzung ist dabei stets, dass die Maschinen und Anlagen in der Lage sind, Ereignisse und Zustände real mithilfe von Sensoren analog zu erfassen, diese Informationen in digitale Daten zu verwandeln und dann an ein übergeordnetes System weiterzugeben.
Viele Projekte scheitern, weil sich Unternehmen auf das reine Sammeln von Daten beschränken. Daten alleine schaffen jedoch noch keinen Mehrwert – auf die konkreten Anwendungsfälle kommt es an.
Lumir Boureanu
Aber die Daten müssen nicht nur erfasst, sondern dann auch sinnvoll verarbeitet werden. Insofern geht es bei einem auf die Digitalisierung der Produktion ausgerichteten Retrofit darum, die Maschinen in den digitalen Produktionsprozess zu integrieren.
Dennoch scheitern viele Projekte, weil sich Unternehmen auf das reine Sammeln von Daten beschränken. Daten alleine jedoch schaffen noch lange keinen Mehrwert – auf die konkreten Anwendungsfälle kommt es an. Wichtig ist deshalb, nicht nur die vorhandenen Daten zu betrachten, sondern auch zu überlegen, welche Informationen wirklich gebraucht werden, um das Potenzial zu heben.
Am Anfang steht sicherlich die Analyse der Fähigkeiten der jeweiligen Maschinen und Anlagen. Fragen wie „Sind schon moderne BUS-Systeme integriert, oder nicht?“ müssen nun beantwortet werden, um den Aufwand der Implementierung einzuschätzen. Dann sollten die Auswahl der Sensoren und die Entwicklung einer Retrofit-Strategie angegangen werden. Die Sensoren werden je nach Bedarf und Ziel des Unternehmens und des Maschinentyps ausgewählt.
Dadurch werden Technologie- und Prozessinformationen durchgängig erfasst und bereitgestellt. Damit zum Beispiel eine Prognose über eine Maschine abgegeben werden kann, müssen Daten über den Zustand der Maschine gesammelt werden. Nach einer professionellen Ist-Analyse wird sie deshalb mit verschiedenen Sensoren ausgestattet. Dies können zum Beispiel Temperatursensoren, Vibrationssensoren und Körperschallsensoren sein. Abnutzung und Verschleiß von wichtigen Maschinenbauteilen können jetzt analog erfasst werden.
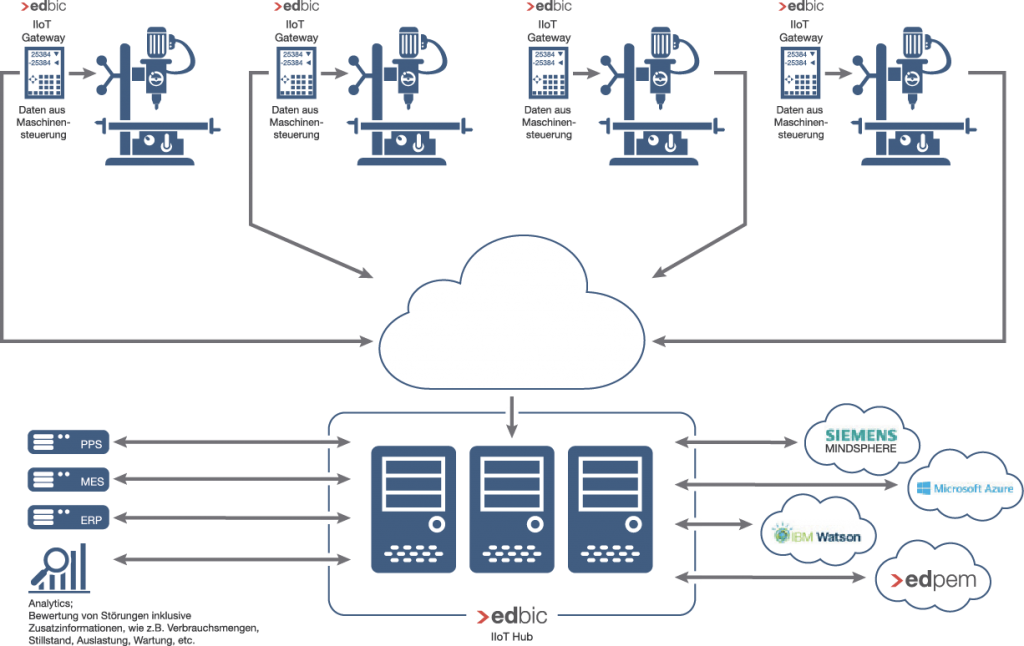
Die ankommenden analogen Signale werden zunächst digitalisiert. Dies passiert mithilfe der Installation der vBox unseres Technologiepartners Fraunhofer-Institut für Produktionstechnologie IPT. Sie arbeitet gemäß den aktuellen Industriestandards: Das kompakte System kann Positionsdaten ebenso wie digitale In- und Outputs mit Sensordaten synchronisieren und dem Anwender nach Bedarf visuell darstellen – unabhängig von der verwendeten Steuerungstechnik.
Um die Daten zu erfassen, aufzubereiten und analysieren zu können, ist die Implementierung von edbic, einer Plattform zur Integration und Interpretation nötig. Denn erst dann können diese Daten genutzt werden, um Condition Monitoring zu betreiben, das in Echtzeit Auskunft über den aktuellen Zustand der Maschine gibt.
Es können Produktions- und Werkmaschinen, Anlagen, Verarbeitungszentren, Geräte, aber auch unterschiedliche Industrieprotokolle, OPC UA, Siemens S7, sowie Cloud-Services in edbic zusammengeführt und integriert werden. Ebenso können Prozesse und andere Workflows orchestriert und die dazugehörigen Daten in einem Dashboard gespeichert, angezeigt und analysiert werden.
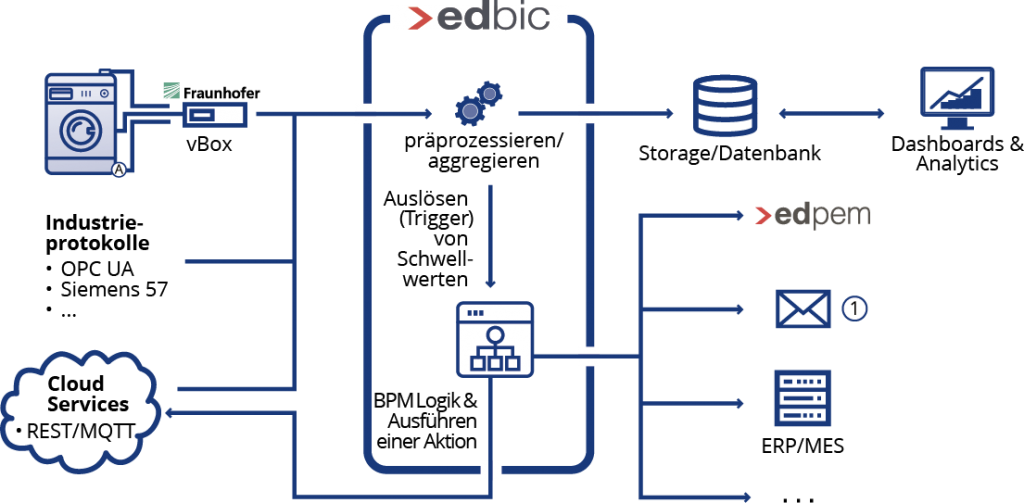
edpem, ein „Process Event Monitoring“-System, visualisiert die „rohen“ Daten im Controlling Dashboard, alarmiert, wenn Schwellwerte überschritten werden, und verschickt E-Mails oder Slack-Nachrichten bei Anomalien. Genauso gut können aber auch die Daten in das vorhandene ERP- oder MES-System gesendet werden. Vielleicht starten Sie sogar mit einem Pilotprojekt, also zunächst mit einer kleinen Anzahl an Maschinen. So kann der Maschinenpark sukzessiv harmonisiert und vernetzt sowie eine Kommunikation möglich gemacht werden.
Deshalb lohnt sich digitaler Retrofit
- Retrofit schafft die Basis für die Digitalisierung der Produktion, indem Maschinen und Anlagen in digitale Prozesse integriert werden.
- Retrofit sorgt für Investitionssicherheit, weil bereits angeschaffte Maschinen und Anlagen weiter genutzt werden können.
- Im Vergleich zur Neuanschaffung eines Assets ist Retrofit äußerst günstig.
- Durch Retrofit werden digitale Szenarien möglich – und das bedeutet mehr Transparenz, steigende Effektivität, Effizienz sowie Flexibilität bei den Prozessen und innovativen Use-Cases.
- Retrofit trägt zu einer längeren Maschinenlebensdauer durch die permanente Überwachung der Maschinen und bessere Ersatzteilversorgung bei.
Der Hauptunterschied und damit ein großer Vorteil bei der von uns beschriebenen Retrofit-Methode ist die stabile Komplexität. Sie steigt nicht mit der Anzahl der Maschinen, sondern bleibt aufgrund des Business-Integration-Clusters, edbic, tragfähig. Das macht auch Ihr digitales Projekt um vieles leichter und agiler. Folgenden Tipp möchten wir Ihnen noch an die Hand geben: Wenn Sie wirklich die Hebel der Digitalisierung nutzen möchten, dann sollten Sie sich auch mit Ihren Partnern, Kunden und Lieferanten verbinden und zusammenarbeiten. Nur so kann ein effizientes Ecosystem entstehen, das für alle Seiten einen Mehrwert schafft! //
Kontakt zum Autor
Namensnennung – Weitergabe unter gleichen Bedingungen 3.0 Deutschland (CC BY-SA 3.0 DE)
Dies ist eine allgemeinverständliche Zusammenfassung der Lizenz (die diese nicht ersetzt).
Sie dürfen:
Teilen — das Material in jedwedem Format oder Medium vervielfältigen und weiterverbreiten
Bearbeiten — das Material remixen, verändern und darauf aufbauen
und zwar für beliebige Zwecke, sogar kommerziell.
Der Lizenzgeber kann diese Freiheiten nicht widerrufen solange Sie sich an die Lizenzbedingungen halten.
Unter folgenden Bedingungen:
Namensnennung — Sie müssen angemessene Urheber- und Rechteangaben machen, einen Link zur Lizenz beifügen und angeben, ob Änderungen vorgenommen wurden. Diese Angaben dürfen in jeder angemessenen Art und Weise gemacht werden, allerdings nicht so, dass der Eindruck entsteht, der Lizenzgeber unterstütze gerade Sie oder Ihre Nutzung besonders.
Weitergabe unter gleichen Bedingungen — Wenn Sie das Material remixen, verändern oder anderweitig direkt darauf aufbauen, dürfen Sie Ihre Beiträge nur unter derselben Lizenz wie das Original verbreiten.
Keine weiteren Einschränkungen — Sie dürfen keine zusätzlichen Klauseln oder technische Verfahren einsetzen, die anderen rechtlich irgendetwas untersagen, was die Lizenz erlaubt.