Aufbruch ins IIoT: Wie bestehende Anlagen zukunftsfit werden.
Über den Weg hin zur Predictive Maintenance sprach die Redaktion mit Lumir Boureanu, CEO der compacer GmbH.
Herr Boureanu, wie unterstützen Sie Ihre Kunden bei der Erfassung, Konsolidierung und Auswertung heterogener Maschinendaten?
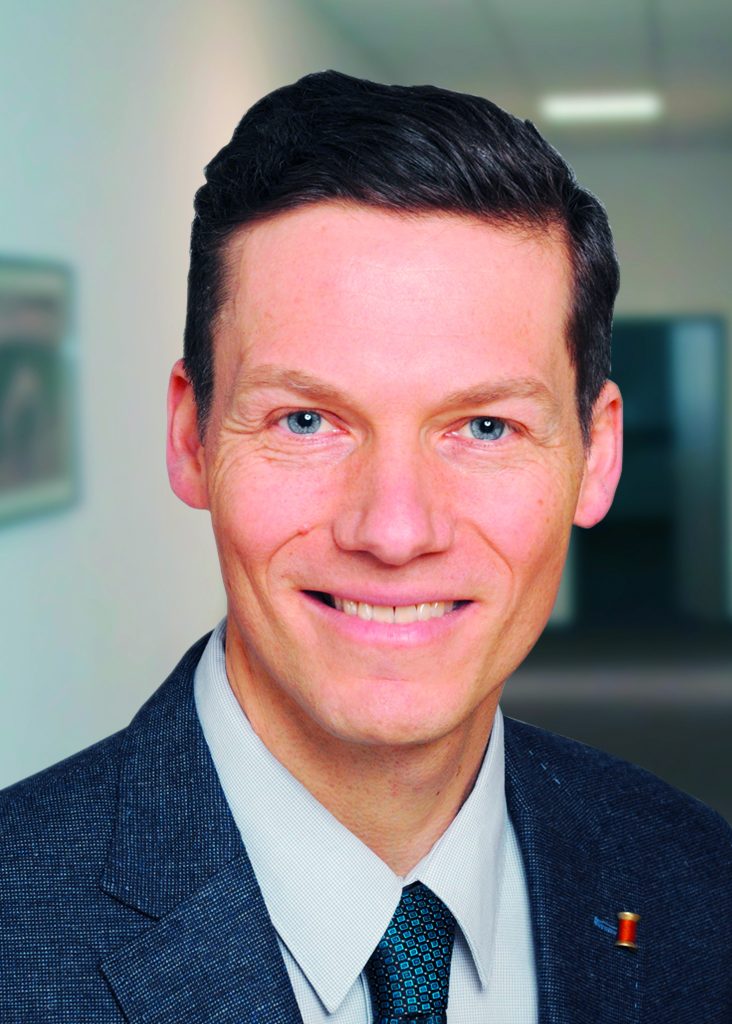
Mittlerweile liegen viele Daten aus Maschinen und Anlagenparks in deutschen Unternehmen vor. Es ist aber nicht die Frage, ob Unternehmen bereits einen Datenbestand haben, sondern wie die mannigfaltigen Maschinendaten genutzt werden, um neue Erkenntnisse daraus zu gewinnen. Eine Herausforderung stellt vor allem der Medienbruch dar, wenn die Daten aus Maschinen an ERP-Lösungen übergeben werden sollen, um weiter Analysen und Prozesse anzustoßen. Gerade im Maschinen- und Anlagenbau muss der Medienbruch gemeistert werden, um die Anlagen fit für das IIoT zu machen.
Wie sieht in diesem Kontext Ihre Lösung aus?
Nach einer professionellen Ist-Analyse wird die Maschine mit verschiedenen Sensoren ausgestattet. Zum Beispiel mit einem Temperatursensor, einem Vibrationssensor und einem Körperschallsensor. Anschließend werden die generierten analogen Signale über die vBox vom Fraunhofer Institut in digitale Daten umgewandelt. Um diese Daten zu erfassen, aufzubereiten und analysieren zu können, ist nun die Implementierung von „edbic“, unserer Plattform zur Integration und Interpretation, nötig. Denn erst jetzt können diese Daten genutzt werden, um Condition Monitoring zu betreiben, das in Echtzeit Auskunft über den aktuellen Zustand der Maschine gibt.
Was ist und wie funktioniert eigentlich „edbic“?
edbic ist ein modernes Datenintegrationssystem, das alle Beteiligten innerhalb der Wertschöpfungskette miteinander verbindet. Alle Daten unterschiedlicher Formate und Herkunft laufen in edbic zusammen. Mit dieser Middleware können wir Produktions- und Werkmaschinen, Anlagen, Verarbeitungszentren, Geräte, aber auch unterschiedliche Industrieprotokolle wie OPC-UA, Siemens S7 sowie diverse Cloud-Services zusammenführen und integrieren. Ebenso können Prozesse und andere Workflows orchestriert und die dazugehörigen Daten in einem Dashboard gespeichert, angezeigt und analysiert werden. Anschließend kommt unser Tool „edpem“ zum Einsatz.
Das „Process Event Monitoring“-System visualisiert die „rohen“ Daten im Controlling Dashboard und alarmiert, wenn Schwellwerte überschritten werden. Bei registrierten Anomalien verschickt „edpem“ E-Mails oder Slack-Nachrichten. Genauso gut können aber auch die Daten in das vorhandene ERP- oder MES-System gesendet werden. Durch diese sinnvolle Automatisierung werden bestehende Geschäftsprozesse nachhaltig verbessert und für mehr Übersichtlichkeit und Stabilität gesorgt.
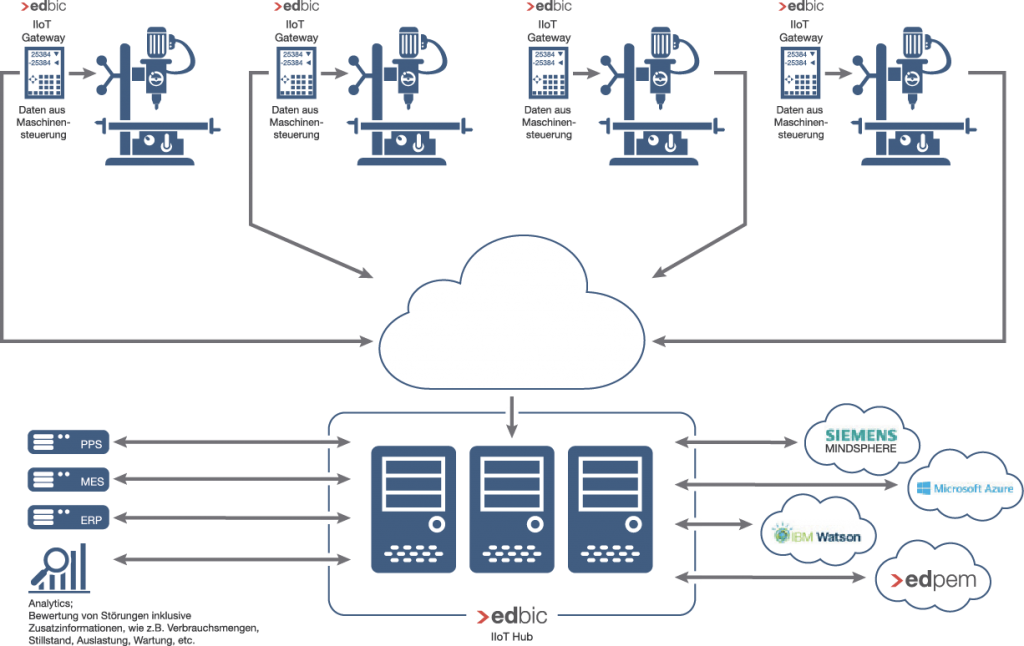
Welche Nutzungsmodelle sind vorgesehen?
Wir bieten unseren Kunden Managed Services, Software as a Service oder On-premise-Implementierungen an. Als Unternehmen der eurodata-Gruppe nutzen wir das eurodata-eigene Hochleistungs-Rechenzentrum in Saarbrücken, das nach ISO/IEC 27001 zertifiziert ist.
Der nächste Schritt in Richtung Smart Factory wird nach einem längeren Beobachtungszeitraum realisiert: Nach der Erhebung entsprechender Vergleichsdaten, die sich aus den Monitoring-Daten ergeben, lassen sich Zustandsprognosen ableiten und ein Frühwarnsystem etablieren.
Sind wir jetzt schon bei der Smart Factory?
Durch diese Maßnahmen sind unsere Kunden der Smart Factory bereits ein großes Stück näher gekommen, in jedem Fall sind aus den gewonnenen Daten bereits neue Geschäftspotenziale gewachsen.
Der nächste Schritt in Richtung Smart Factory wird nach einem längeren Beobachtungszeitraum realisiert: Nach der Erhebung entsprechender Vergleichsdaten, die sich aus den Monitoring-Daten ergeben, lassen sich Zustandsprognosen ableiten und ein Frühwarnsystem etablieren. Dadurch werden zukünftig Anomalien, Abnutzungserscheinungen, Ausfälle oder andere Probleme innerhalb des Produktionsprozesses rechtzeitig identifiziert. Sobald genügend Daten vorliegen, geht es weiter in Richtung Predictive Maintenance.
Und wie geht es weiter für Ihr Haus?
Angesichts der Tatsache, dass die Erfassung, Konsolidierung und Auswertung heterogener Maschinendaten und deren Übergabe an ERP-Systeme in den nächsten Jahren die Erfolgsgrundlage von Maschinen- und Anlagenbauern bleiben wird, freue ich mich auf viele neue Projekte. //
Kontakt zum Autor
Namensnennung – Weitergabe unter gleichen Bedingungen 3.0 Deutschland (CC BY-SA 3.0 DE)
Dies ist eine allgemeinverständliche Zusammenfassung der Lizenz (die diese nicht ersetzt).
Sie dürfen:
Teilen — das Material in jedwedem Format oder Medium vervielfältigen und weiterverbreiten
Bearbeiten — das Material remixen, verändern und darauf aufbauen
und zwar für beliebige Zwecke, sogar kommerziell.
Der Lizenzgeber kann diese Freiheiten nicht widerrufen solange Sie sich an die Lizenzbedingungen halten.
Unter folgenden Bedingungen:
Namensnennung — Sie müssen angemessene Urheber- und Rechteangaben machen, einen Link zur Lizenz beifügen und angeben, ob Änderungen vorgenommen wurden. Diese Angaben dürfen in jeder angemessenen Art und Weise gemacht werden, allerdings nicht so, dass der Eindruck entsteht, der Lizenzgeber unterstütze gerade Sie oder Ihre Nutzung besonders.
Weitergabe unter gleichen Bedingungen — Wenn Sie das Material remixen, verändern oder anderweitig direkt darauf aufbauen, dürfen Sie Ihre Beiträge nur unter derselben Lizenz wie das Original verbreiten.
Keine weiteren Einschränkungen — Sie dürfen keine zusätzlichen Klauseln oder technische Verfahren einsetzen, die anderen rechtlich irgendetwas untersagen, was die Lizenz erlaubt.